
今年3月,2024年中国百强产业集群名单公布,泉州机械装备产业集群上榜。作为九大千亿集群产业之一,泉州的机械装备产业正向高端化、智能化、绿色化发展,产值规模已超2600亿元,拥有规上机械装备企业700多家,超亿元企业300多家。
铸造是工业领域最传统、最古老的细分行业,是装备制造中不可或缺的一环。
坐落于泉州南安,全球首座万吨级铸造3D打印全流程智能工厂——国家智能铸造产业创新(泉州)中心(以下简称“共享泉州中心”),正用不断迭代的3D打印技术改变行业,向全国乃至全世界的合作伙伴提供砂型3D打印、快速铸造服务、智能制造(铸造)系统解决方案以及各类零部件精加工服务。
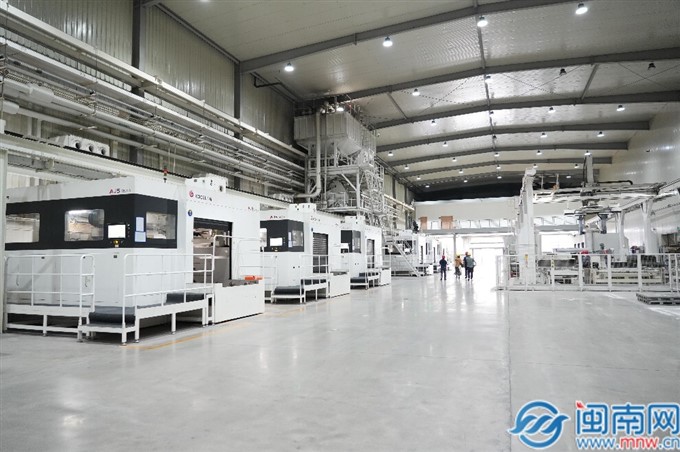
不同于传统车间,共享中心的车间干净整洁
谈到铸造厂,大多与“傻大黑粗”挂钩,存在着生产能耗高,智能化、自动化水平低以及产品合格率低等问题,人在车间里走上一圈,白衬衫的领子和鼻口都会变黑。但共享泉州中心的智能车间,是截然不同的画面:放眼望去宽敞、整洁、明净,成形工厂现场只有四五名工人,AVG小车根据指令在车间交通道上运输工作箱,一幢幢像小房子的3D打印设备有序排开,各自“在家”执行着生产任务。
制砂不见砂,车间的砂罐设置在屋顶上,经由管道运输到各个打印机,接到指令后,铺砂器开始操作,每铺设一层砂,打印头就喷射一层墨水,并在树脂和固化剂的作用下形成砂芯的横截面形状。“计划打印1416层,目前已经打印了811层,层耗时14秒……”屏幕实时显示当前的进度以及打印室的温度、湿度、 气压以及墨水温度、压力等参数,就这样经过千层的堆叠,砂芯才算打印完成。
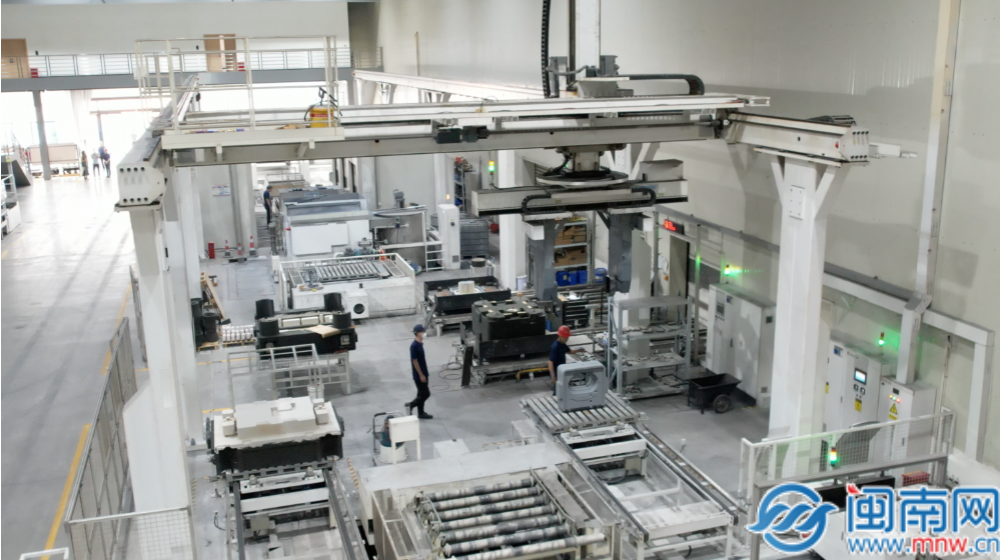
3D打印车间内工人正有序作业
“传统的铸造成形方式要先制作模具,需要制芯、造型、合箱很多工序,周期较长,而3D打印成形只要一道工序就能解决问题。”中心副总经理、营销部长田鑫说,传统铸件小件的生产从工艺设计到产品完成需要30天到60天,而中心的全流程绿色智能工厂,7天到20天就能交付,解决了模具制备周期长、成本高和成品率低等难题,还让车间实现了无吊车、无模型、无重体力劳动、无废砂及粉尘排放、无温差的“五无”生产模式。
曾经的“傻大黑粗”,在这里摇身一变成了“窈窕淑女”。
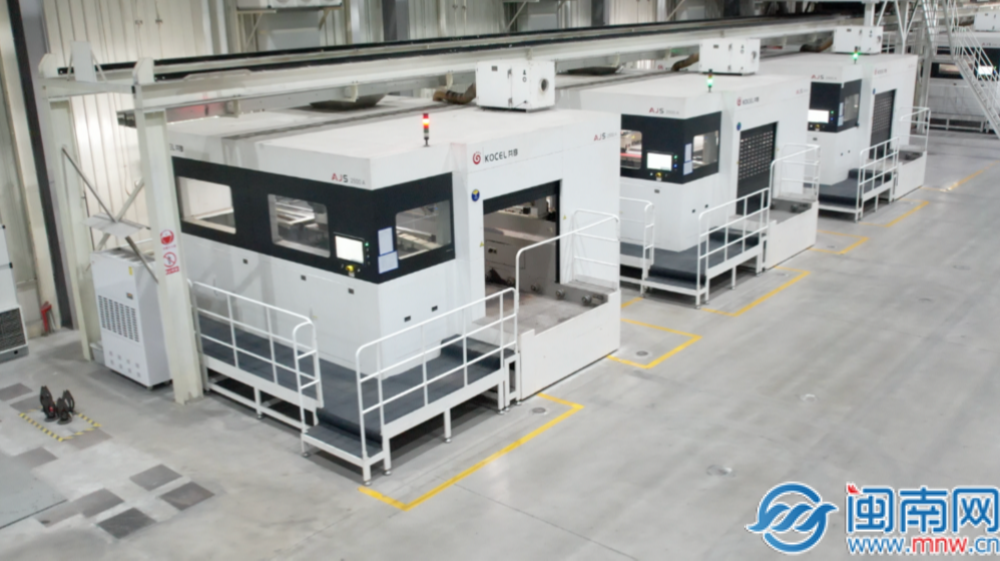
车间内正有序作业的3D打印机
那么,基于3D打印的铸造有哪些流程呢?田鑫说,从设计前端开始,整个生产流程要先在电脑系统里进行“虚拟制造”,确认无误后才能投产。根据设定,生产集成系统会驱动智能设备,每个生产环节的参数将及时回传,与数据库、知识库、专家库对比,进行自动纠偏或者人工干预,以确保产品的合格率和精度。得益于数字化、智能化,中心铸件的生产效率可以达到同等规模传统铸造的3倍以上。
“我们公司的总部设在宁夏银川,最早是给机床厂做铸件的,后来决定以3D打印为突破口谋求转型,前后累计投入10多亿元进行研发,拥有全球最大的3D打印设备,自主研发的机器还反向出口到欧洲、日本。”在田鑫看来,新材料、新工艺、新设备的使用,是传统企业发展新质生产力的方式。共享泉州中心的生产车间启用了智能化生产线后,对前端的工艺设计提出了更高的要求,同时,他们在后端加入了生产管理和企业运营软件等,建成了一套覆盖生产前、中、后的智能化制造和管理体系。
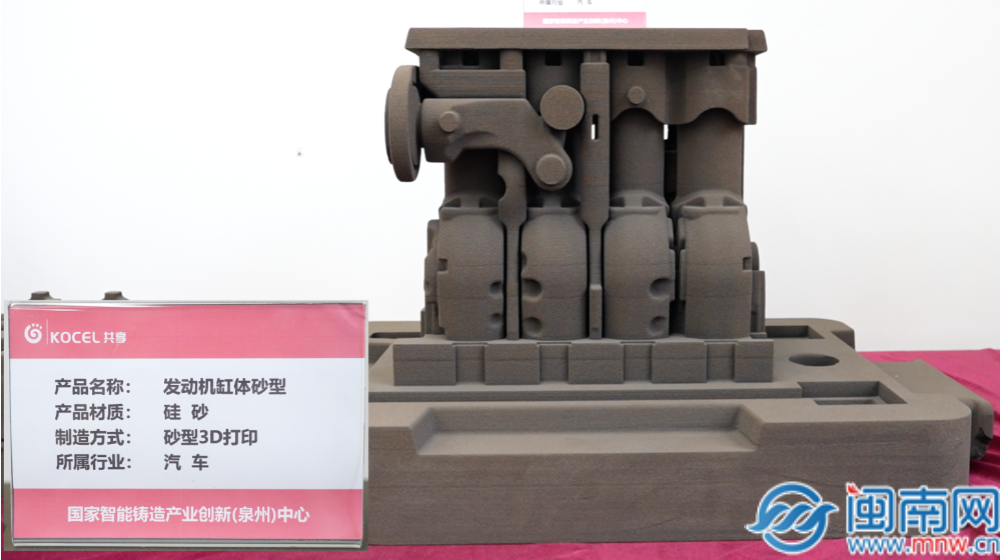
由砂型3D打印的发动机缸体砂型
去年3月份,共享泉州中心进入试生产阶段,启用了6台打印设备,每个月的产能约为600吨砂型、200吨铸造。目前主营的3D打印产品为机械、能源、工业压缩机、泵阀等,打印材料涵盖石英砂、硅砂、陶瓷砂等,产品精度达到±0.35mm,即一粒沙的厚度。
据了解,中心后续将按规划陆续增加4台打印设备,“十四五”期间进一步释放产能,达到年产1万吨砂型、5000吨铸件的产能的目标,并实现年销售收入达1亿元以上。
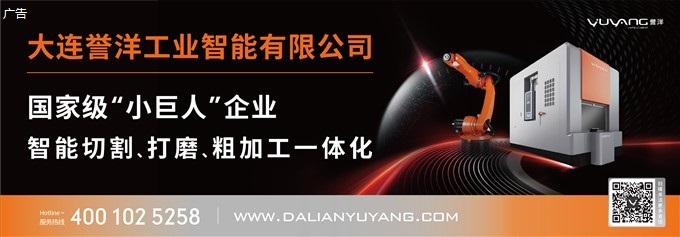
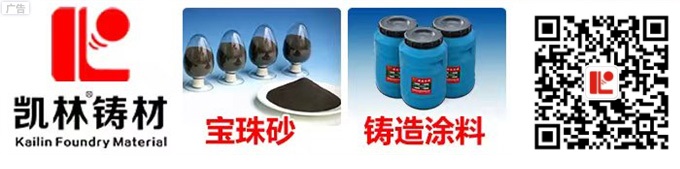
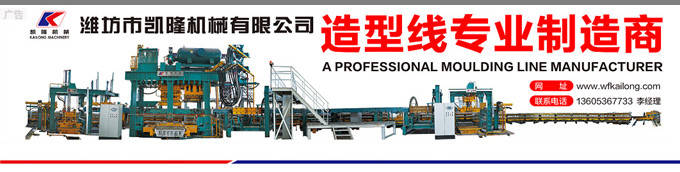
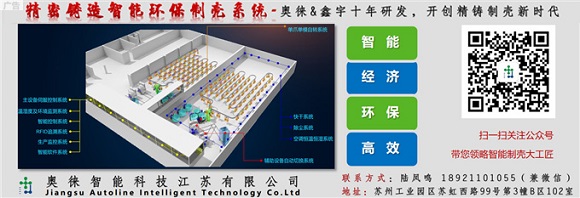
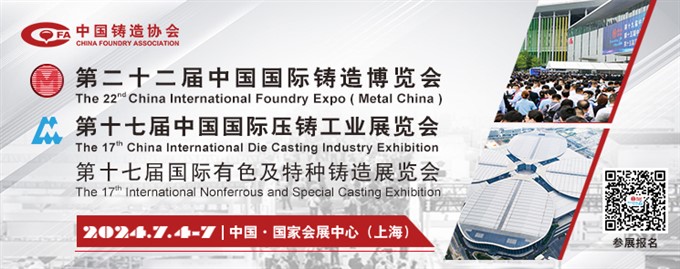
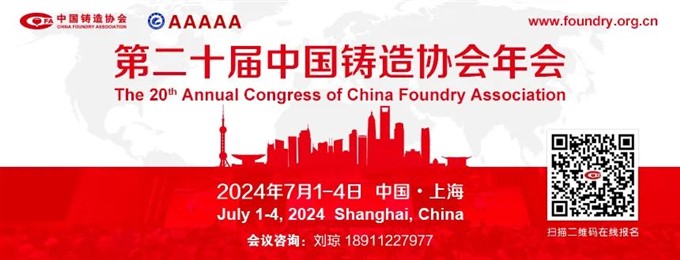
/*本文部分内容(图片)来源于网络,若牵涉版权请联系删除。
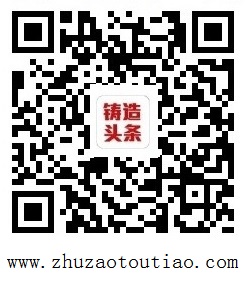
——欢迎登陆www.zhuzaotoutiao.com发表您的作品
没有账号?点击 注册